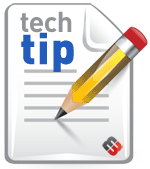
Single component, no mix epoxies are gaining increasing popularity over traditional two component systems. They are commonly employed in bonding, sealing, coating and potting applications. These systems are precatalyzed and require only moderate heat to cure.
This avoids the need to mix two components which can result in air entrapment. To prevent such problems, two part epoxies often must be mixed in vacuum environments. Additionally, two component systems often have different multiple mix ratios, e.g. ten to one by weight and limited pot lives. This often leads to errors. One part, no mix systems alleviate inaccurate mixing and eliminate waste from non-use of compounds in specified time periods. Furthermore, the speed of cure is rapid, often faster than two part systems.
The performance profile of one part epoxy systems is truly outstanding. These formulations exhibit high physical strength, superior chemical and temperature resistance and excellent adhesion to both similar and dissimilar substrates. They have extremely low shrinkage upon cure and resist exposure to thermal cycling. Grades are available that have superior thermal conductivity, electrical conductivity and electrical insulation properties. Special compounds meet NASA low outgassing specifications and are USP Class VI approved.
In order to meet the increasing needs of industry, Master Bond has placed an emphasis on the development of new formulations. Particularly noteworthy is Master Bond
EP17, a toughened, high temperature resistant compound for exposure up to 600°F. It has high dimensional stability and will resist exposure to hostile chemicals. Master Bond
Supreme 10HTFL offers a T-peel strength in excess of 60 pli for aluminum bonding and can withstand shock and vibration. Another unique system is Master Bond
Supreme 3HT-80. It is designed to cure within 30 minutes at 175°F (80°C) and offers high strength properties.